Spiderbot transform into rolling wheel: Witness the incredible metamorphosis of a futuristic spider-like robot as it seamlessly transitions into a rolling sphere. This isn’t your grandpappy’s clunky bot; we’re talking about a marvel of engineering, a testament to adaptable locomotion, and a glimpse into the future of robotics. Prepare to be amazed as we delve into the mechanics, the challenges, and the sheer brilliance behind this transformative technology.
From its initial spider-like gait to its smooth rolling motion, the Spiderbot’s transformation is a study in dynamic engineering. We’ll explore the intricate mechanisms that allow for this shape-shifting feat, the materials science behind its robust design, and the potential applications that span diverse terrains and tasks. Get ready to uncover the secrets of this revolutionary robot!
Spiderbot Morphology and Transformation
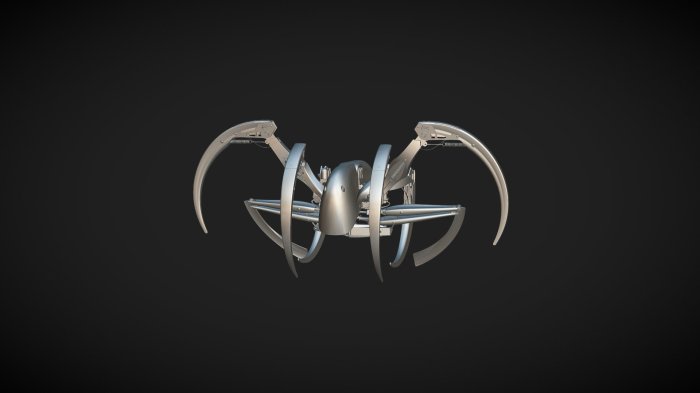
Source: sketchfab.com
The Spiderbot, in its initial configuration, resembles a highly articulated arachnid. Eight independently controlled legs, each ending in a gripper, provide exceptional maneuverability across varied terrains. A central chassis houses the processing unit, power source, and transformation mechanisms. Its low center of gravity ensures stability during locomotion in its spider form. The transition to a rolling wheel configuration is a marvel of miniature engineering.
The transformation from a multi-legged spider to a single-wheeled robot is a complex process involving a series of precisely coordinated movements. Hydraulic actuators retract the spider legs, simultaneously pivoting them inward towards the chassis. These legs then fold neatly into the body, forming a streamlined, aerodynamic profile around a central, newly revealed wheel. This wheel, previously concealed within the chassis, is constructed from a lightweight yet durable composite material. The transformation is powered by a compact, high-torque motor system.
Spiderbot Center of Gravity Shift During Transformation
The center of gravity shifts dramatically during the transformation. In spider mode, the center of gravity is low and distributed across the eight legs, providing excellent stability, even on uneven surfaces. As the legs retract, the center of gravity rises and shifts towards the central axis of the newly formed wheel. This shift is carefully managed by the onboard control system to prevent tipping during the transformation sequence. The final center of gravity in wheel mode is significantly higher, making the bot more susceptible to lateral forces.
Stability Comparison: Spider vs. Wheel Form
The Spiderbot exhibits drastically different stability characteristics in its two forms. In spider form, its low center of gravity and multiple points of contact with the ground result in high stability and exceptional maneuverability across uneven terrain. Think of a spider effortlessly navigating a complex web – that’s the Spiderbot’s spider form in action. However, in wheel mode, its stability is significantly reduced. The high center of gravity and single point of contact make it more susceptible to tipping, particularly when encountering inclines or uneven surfaces. Imagine a unicycle – that’s a good analogy for the reduced stability in wheel form.
Internal Transformation Mechanisms Diagram
Imagine a cross-section of the Spiderbot. The central chassis is a roughly cylindrical core containing the main processing unit and power source. Surrounding this core are eight independently articulated legs, each with its own hydraulic actuator and folding mechanism. These actuators are controlled by the onboard computer, triggering the precise sequence of movements for transformation. Concealed within the chassis is a robust wheel, constructed from a high-strength composite material. During transformation, the legs retract inwards, folding neatly against the chassis, while the wheel is simultaneously deployed. A series of gears and linkages coordinate the leg retraction and wheel deployment, ensuring a smooth and controlled transition. The entire mechanism is remarkably compact, a testament to sophisticated miniaturization.
Wheel Mode Functionality
Spiderbot’s transformation into a rolling wheel isn’t just a cool trick; it’s a strategic shift in locomotion offering significant advantages in specific situations. This mode leverages the efficiency of a circular form for traversing certain terrains and accomplishing particular tasks, while simultaneously presenting certain limitations compared to its multi-legged counterpart.
The rolling wheel form provides superior speed and efficiency over flat, even surfaces. This is due to the minimized friction and streamlined movement compared to the complex leg articulation of the spider form. Think of a bicycle versus walking – the bicycle, analogous to the wheel mode, is clearly faster and more energy-efficient on paved roads.
Advantages of Wheel Locomotion
The streamlined design of the wheel mode drastically reduces friction, resulting in faster traversal across smooth surfaces. This translates directly to increased speed and reduced energy consumption compared to the spider mode, where each leg movement requires individual power expenditure. The simple rolling motion is inherently more efficient for long-distance travel on suitable terrain.
Limitations of Wheel Locomotion
The wheel mode’s simplicity is also its downfall. Its inability to traverse uneven terrain or obstacles is a major limitation. Unlike the spider’s articulated legs, which can adapt to irregularities in the ground, the wheel is restricted to surfaces that allow for continuous rolling motion. A single rock or significant incline can completely halt progress, a problem easily overcome by the spider’s adaptable gait. Furthermore, maneuverability is severely restricted; turning requires a wider radius than the agile movements possible in spider mode.
Applications of Wheel Mode in Different Environments
The wheel mode finds its niche in environments characterized by smooth, relatively flat surfaces. Imagine Spiderbot deployed in a warehouse, efficiently navigating aisles to transport goods. The speed and efficiency of wheel locomotion would significantly improve its operational speed compared to its slower, more cumbersome spider form. Similarly, a smooth, flat surface like a paved road would also be ideal for long-distance travel. Consider scenarios requiring rapid transport of small payloads across such terrains.
Efficiency Enhancement in Specific Tasks
In material handling scenarios, the wheel mode shines. Imagine Spiderbot tasked with moving packages across a warehouse floor. The speed advantage of wheel mode significantly reduces the overall time required for these tasks, boosting productivity. Similarly, transporting small sensors or monitoring equipment across a flat, outdoor area would benefit from the efficiency and speed offered by the wheel form.
Crucial Scenario for Wheel Mode Success
Consider a scenario where Spiderbot is deployed in a post-disaster environment, needing to quickly transport vital medical supplies across a relatively flat, but damaged, road. The spider mode, while more adaptable to rubble, would be far slower. The wheel mode, however, would allow for rapid delivery of life-saving resources, highlighting its crucial role in time-sensitive situations where speed is paramount. The ability to swiftly traverse long distances on relatively flat terrain makes the wheel mode indispensable in this emergency context.
Transformation Process and Control: Spiderbot Transform Into Rolling Wheel

Source: artstation.com
Imagine a spiderbot, all spindly legs, suddenly morphing into a sleek, rolling wheel – a seriously cool transformation, right? This adaptability reminds me of how important device verification is; if your device isn’t verified, you might find yourself locked out of Google apps, as explained in this article about google block unverified devices google apps. Just like the spiderbot needs to adapt its form, we need to ensure our devices are properly authorized for seamless access.
Back to our rolling spiderbot – now that’s what I call future-proof design!
Spiderbot’s transformation from a six-legged arachnid to a rolling wheel is a complex process demanding precise coordination and significant energy management. This section delves into the intricacies of this transformation, exploring the energy requirements, control systems, potential failure points, and a step-by-step guide to the process itself. Understanding these aspects is crucial for optimizing the bot’s performance and reliability.
Energy Requirements for Transformation
The energy consumed during Spiderbot’s transformation is substantial, primarily due to the intricate movements of numerous actuators and the repositioning of its body segments. This energy demand is dependent on several factors including the speed of transformation, the efficiency of the actuators, and the overall weight of the robot. We can estimate the energy consumption using a simplified model, considering the work done by each actuator during the transformation. For instance, each leg needs to fold, rotate, and possibly retract, requiring energy proportional to the torque and angular displacement involved. The energy source, likely a high-capacity battery, needs to be adequately sized to handle these demands, with considerations for thermal management to prevent overheating during rapid transformations. Real-world examples, such as the energy consumption of similar robotic systems undergoing complex shape-shifting, can help in predicting the energy requirements for Spiderbot’s transformation.
Control Systems for Smooth and Reliable Transformation
A robust control system is paramount for a smooth and reliable transformation. This system would likely involve a hierarchical control architecture, with high-level controllers overseeing the overall transformation sequence and low-level controllers managing individual actuators. Sensor feedback, including position sensors, force sensors, and possibly vision systems, is crucial for accurate control and error correction. The system must account for various factors like friction, inertia, and potential external forces to ensure precise movements and prevent damage. Sophisticated algorithms, potentially incorporating techniques like model predictive control, are necessary to optimize the transformation process, minimizing energy consumption and ensuring a consistent, smooth transition. A real-world analogy could be the complex control systems found in advanced industrial robots that perform delicate and precise assembly tasks.
Potential Failure Points and Solutions
Several potential failure points exist within Spiderbot’s transformation mechanism. Mechanical wear and tear on actuators and joints, especially under repeated transformations, is a primary concern. Solutions include the use of durable, high-quality materials, regular maintenance, and the incorporation of redundancy mechanisms. Software glitches or sensor failures can also disrupt the transformation process. Robust error detection and recovery mechanisms, combined with redundant sensors and fail-safe protocols, can mitigate these risks. Power supply issues, such as battery depletion or short circuits, could halt the transformation mid-process. Redundant power sources and efficient power management strategies are essential safeguards. Finally, unforeseen obstacles or external forces during the transformation could lead to malfunctions. Improved sensor feedback and adaptive control algorithms can help the system react and adjust to unexpected events.
Step-by-Step Guide to Transformation Initiation and Control
The transformation process begins with a high-level command initiating the sequence. The control system then sequentially activates individual actuators, following a pre-programmed trajectory. First, the legs are retracted and folded inwards. Simultaneously, the wheel mechanism begins to unfold and rotate. As the legs are fully retracted, the body shifts its center of gravity to align with the wheel’s axis. Finally, the wheel locks into its operational position, completing the transformation. The control system continuously monitors sensor feedback, adjusting actuator movements in real-time to compensate for any deviations from the planned trajectory. Safety protocols are implemented throughout the process to prevent damage or unexpected behavior.
Effect of Varying Speeds on Transformation
Varying the speed of transformation impacts several aspects of the process. Slower transformations allow for more precise control and reduce the risk of mechanical stress on components, potentially increasing the lifespan of the system. However, slower transformations also increase the overall time required for the process. Faster transformations can be advantageous in situations where rapid response is needed but increase the risk of component wear and tear and require more robust control systems to maintain stability and accuracy. The optimal transformation speed is a balance between efficiency and reliability, which may need to be adjusted based on the specific operational requirements.
Materials and Engineering
The successful transformation of Spiderbot from a legged configuration to a rolling wheel necessitates careful consideration of materials and a robust engineering design. The choice of materials directly impacts the robot’s weight, strength, durability, and overall efficiency. The engineering challenges lie in creating a mechanism that allows for a smooth, reliable, and rapid transformation while maintaining structural integrity under various conditions.
Material Selection for Spiderbot Components
Selecting appropriate materials for the Spiderbot’s body and wheel components is crucial for optimal performance. The body requires a material that balances strength, lightweight properties, and impact resistance. The wheel components, on the other hand, need to be durable and capable of withstanding the stresses of rolling motion. Lightweight yet strong materials are preferred to minimize energy consumption during locomotion.
Engineering Challenges in Transformation Mechanism Design
Designing a robust and efficient transformation mechanism presents several engineering challenges. The mechanism must be compact to minimize the robot’s overall size and weight, yet capable of handling the significant forces involved in the transformation process. Precision is essential to ensure smooth and reliable operation, preventing jamming or damage to components. The design must also account for potential wear and tear, ensuring longevity and maintainability. Miniaturization and integration of actuators and sensors within the limited space available are further significant design constraints.
Wheel Suspension System Design Approaches
Several approaches exist for designing the Spiderbot’s wheel suspension system. A simple approach involves a rigid connection between the wheel and the robot’s body, offering stability but potentially compromising maneuverability and shock absorption. More sophisticated designs might incorporate spring-based systems, similar to those used in automobiles, providing better shock absorption and improved handling on uneven terrain. Alternatively, a passive suspension system using elastomeric materials could offer a lightweight and compact solution, though potentially with less precise control. The choice of suspension system depends on the desired trade-off between complexity, performance, and weight.
Material Properties Comparison
Material | Strength (Tensile Strength MPa) | Weight (Density g/cm³) | Flexibility (Young’s Modulus GPa) |
---|---|---|---|
Aluminum Alloy 6061 | 276 | 2.7 | 69 |
Carbon Fiber Reinforced Polymer (CFRP) | >1000 (depending on fiber orientation and resin) | 1.6-2.0 | 200-250 |
Titanium Alloy Ti-6Al-4V | 880-1100 | 4.43 | 110 |
High-Strength Steel | >1000 (depending on grade) | 7.85 | 200 |
Spiderbot Component Manufacturing Process
The manufacturing process for the Spiderbot’s components will likely involve a combination of techniques depending on the chosen materials. For example, aluminum alloy parts could be manufactured using CNC machining, while CFRP components might be created using layup techniques followed by curing in an autoclave. 3D printing, particularly using selective laser melting (SLM) or binder jetting, could be used for rapid prototyping and the creation of complex geometries. The precise manufacturing methods will be dictated by factors such as component complexity, material properties, and production volume. High precision is paramount to ensure accurate fit and function of all moving parts within the transformation mechanism.
Environmental Considerations
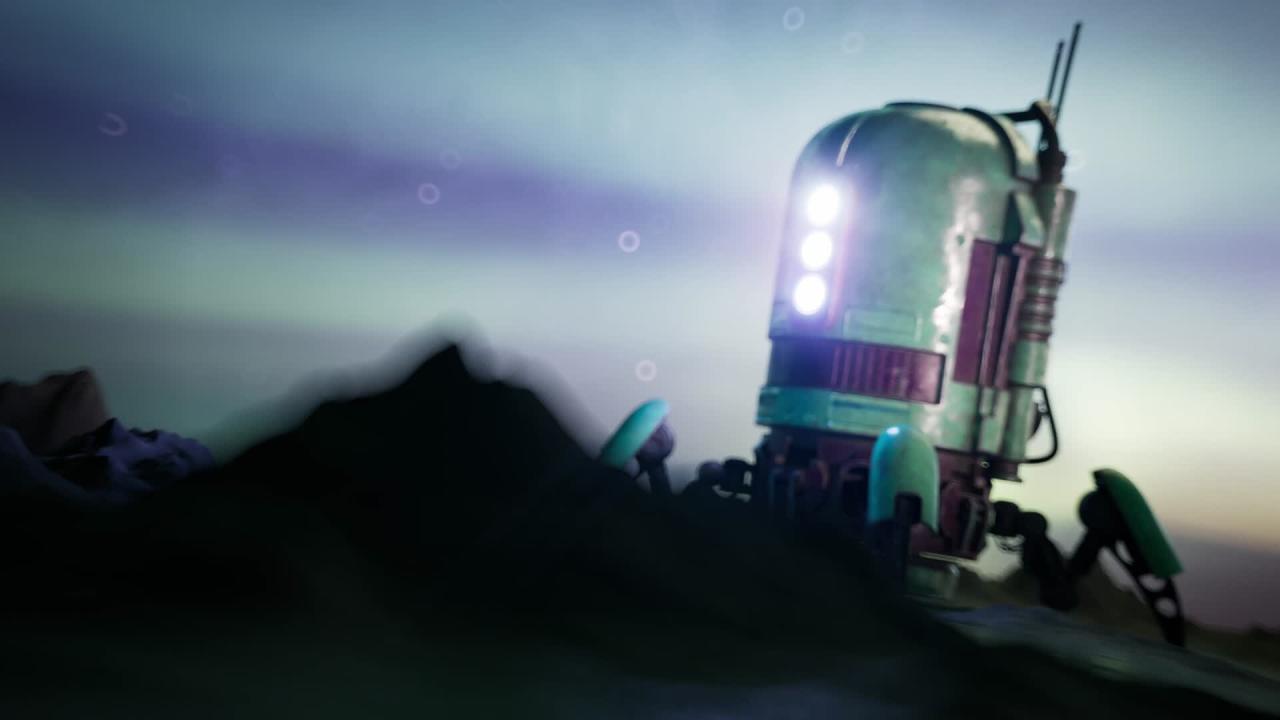
Source: artstation.com
Spiderbot’s functionality extends beyond its impressive transformation capabilities; its design must also consider the diverse environmental conditions it might encounter. Adaptability to various terrains and resilience against environmental hazards are crucial for its successful deployment and operation. This section delves into the environmental considerations shaping Spiderbot’s design and ensuring its sustainable operation.
Spiderbot’s design incorporates features to navigate diverse terrains.
Terrain Adaptability
The Spiderbot’s multi-legged spider configuration provides inherent stability and traction on uneven surfaces, such as rocky terrain or loose soil. In wheel mode, its robust chassis and large diameter wheels allow for efficient traversal of smoother surfaces like roads or pavements. The transition between these modes allows the Spiderbot to seamlessly navigate diverse environments. For instance, the spider legs can provide stability while climbing a steep incline, then the wheel mode can be used for rapid transit across a flat plain. This adaptability is crucial for applications in search and rescue, environmental monitoring, or exploration in challenging environments. The incorporation of sensors and sophisticated control algorithms further enhances the Spiderbot’s ability to assess terrain conditions and adapt its locomotion strategy accordingly.
Surface Interaction and Transformation
The transformation from spider to wheel mode significantly impacts the Spiderbot’s interaction with different surfaces. In spider mode, the numerous points of contact distribute the weight, reducing ground pressure and minimizing the risk of sinking into soft ground. Conversely, wheel mode concentrates the weight, increasing ground pressure, which can be advantageous on hard surfaces but detrimental on soft surfaces. The Spiderbot’s control system manages this by selecting the appropriate mode based on terrain analysis. For example, if the Spiderbot detects soft, unstable ground, it would remain in spider mode to avoid getting stuck. Conversely, when encountering a smooth, hard surface, it would transition to wheel mode for increased speed and efficiency.
Environmental Factor Impacts, Spiderbot transform into rolling wheel
Temperature and humidity are significant environmental factors that influence the Spiderbot’s transformation process and overall functionality. Extreme temperatures can affect the material properties of the Spiderbot’s components, potentially hindering the smooth operation of its actuators and mechanisms. For instance, extreme cold could cause lubricants to thicken, slowing down the transformation process, while extreme heat could lead to component warping or malfunction. Similarly, high humidity can increase the risk of corrosion and damage to electrical components. The Spiderbot’s design incorporates materials and protective coatings that mitigate these risks, ensuring reliable operation within a wide range of environmental conditions. This includes the use of temperature-resistant polymers and sealed electronic enclosures.
Potential Environmental Hazards
The Spiderbot may encounter various environmental hazards during operation, including water, dust, and debris. Ingress of water into the Spiderbot’s internal components can cause short circuits and malfunctions. Dust and debris can accumulate in moving parts, hindering their operation and potentially causing damage. To address these challenges, the Spiderbot’s design incorporates sealing mechanisms, dust filters, and robust components capable of withstanding exposure to harsh environments. Regular maintenance and cleaning protocols are also crucial for ensuring continued functionality. For example, the use of IP67 rated components ensures resistance to dust and temporary submersion in water.
Sustainability Design Considerations
Sustainability is a key design consideration for the Spiderbot. The selection of materials focuses on using recyclable and environmentally friendly components, minimizing the environmental impact of its manufacturing and disposal. The Spiderbot’s energy consumption is optimized through efficient motor design and intelligent power management strategies. Furthermore, the Spiderbot’s design promotes repairability and modularity, extending its lifespan and reducing the need for frequent replacements. For example, the use of readily available and recyclable aluminum alloys reduces the environmental impact of material sourcing. The design also facilitates easy component replacement, minimizing waste and extending the robot’s operational life.
End of Discussion
The Spiderbot’s ability to transform from a multi-legged spider into a rolling wheel represents a significant leap forward in robotic locomotion. Its adaptability to various terrains, coupled with its enhanced efficiency in wheel mode, opens up a world of possibilities for exploration, search and rescue, and even everyday tasks. The engineering challenges overcome in its design highlight the innovative spirit driving the field of robotics, promising even more astonishing advancements in the years to come. This isn’t just a robot; it’s a testament to human ingenuity and the boundless potential of transformative technology.